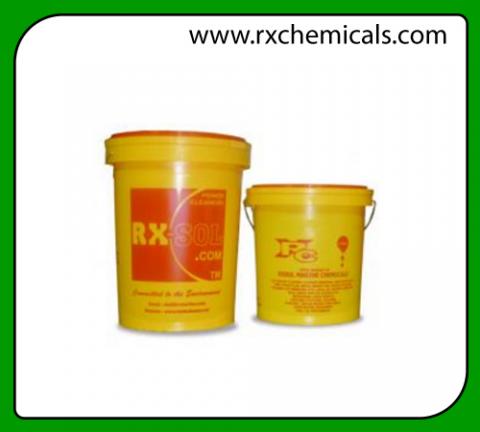
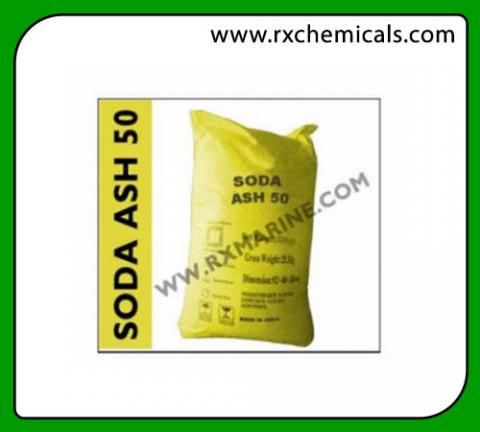
Sodium Sulphite (sulfite) with Catalyst Powder
Catalyzed sodium sulfite for corrosion prevention. Generally speaking, sulfite is not present in natural water. In boiler feedwater conditioning sodium sulfite is fed to a boiler to remove dissolved oxygen and thus prevent pitting. For the reaction between sulfite and oxygen to proceed rapidly and completely, it is necessary to maintain an excess sulfite concentration at an elevated temperature.
Theoretically, 3.5 Kg of chemically pure sodium sulfite are required to remove approx 400 gram of oxygen. The efficiency of the oxygen removal is estimated at 75 per cent to allow for oxidation in contact with air, blowdown losses, etc. Therefore it is estimated that 4.5 Kg of commercial sodium sulfite are required for 450 Gram of oxygen removed (or 10 ppm sulfite per 1 ppm dissolved oxygen.)
The use of sodium sulfite as a chemical deoxygenator is economical within certain limitations imposed by the dissolved oxygen content of the feedwater. If appreciable quantities of dissolved oxygen are permitted to enter the boiler, costs will be high if sulfite is relied on as the sole means of oxygen removal. Generally, costs are balanced by removal of as much of the oxygen as feasible by mechanical means, e.g. deaerator and by using sulfite to react with the residual oxygen.
To prevent corrosion and pitting in feed lines, closed heaters and economizers, it is desirable to feed the sulfite continuously to the boiler feedwater rather than directly to the boiler feedwater rather than directly to the boiler. Reaction between sulfite and oxygen is not instantaneous and the completion of the reaction is aided by the longer contact times provided by feeding sulfite to the feedwater.
Catalyzed sodium sulfite will, however, react almost instantaneously with dissolved oxygen even at cold water temperatures. Because of this property, catalyzed sulfite has found increased use in the treatment of cooling water, process water, distribution system, etc. for preventing oxygen corrosion.
Sodium sulfite anhydrous is a white granular material with the chemical formula Na2SO3
It is primarily used in pulp and paper industry. It is used in water treatment as an oxygen scavenger agent, in the photographic industry to protect developer solutions from oxidation, in textile industry as a bleaching, as a desulfurising and as a dechlorinating agent and in leather trade for the sulfitisation of tanning extracts. It is used in chemical manufacturing as a sulfonation and sulfomethylation agent. It is used in the production of rubber chemicals, sulfur dyes and other chemical compounds. It is used in other applications including ore flotation, oil recovery, food preservative, making dyes, and detergent.
White, free flowing crystalline Odorless powder
Dose of Sulfite can be controlled by this method ::: Because it readily reacts with oxygen to form sulfate, sulfite is not usually found in natural water systems. In its most common form, sodium sulfite, it is widely used as an oxygen scavenger in feedwater conditioning to prevent pitting in boilers; as a pulping or pulp-bleaching agent by the paper industry; to neutralize residual chlorine in potable water, sewage, industrial effluents, and textile process waters; and as a reducing agent in still other manufacturing processes.
Sample water over 100°F will cause a false-high reading; therefore, quickly cool to room temperature before testing. To prevent a false-low reading caused by the reaction between sulfite and ambient air or dissolved oxygen, water samples should be capped while cooling and then tested without delay. An iodometric drop test is the most popular field method for determining sodium sulfite concentrations.
Reagent packs, containing an instruction and chemicals only, may be purchased for use with buret setups. Note: Sulfide and ferrous iron cause positive interference; copper and nitrite cause negative interference.
Sulfite, Titrimetric Method(0-100ppm)
The test for sulfite is based on the colour change end point reaction. At the end point reagent combines with the indicator to form a blue color.
Apparatus Required
Buret, automatic, 25 ml - 1 ( Sample Tube, Graduated, 25 mL, plastic w/cap and white dot )
Casserole porcelain, 210 ml - 1
Cylinder, graduated, 50 ml - 1
Measuring dipper (plastic) - 1
Stirring rod, glass - 1
Chemicals Required
TK - 13 ::: RXSOL-62-5503-002
TK - 14 ::: RXSOL-62-5503-003
TK - 15 ::: RXSOL-62-5503-004 ( 1 ml =0.5 mg SO3 )
Procedure for Test
The water sample should be freshly obtained with as little contact as possible with air. Do not filter the sample, but cool it to room temperature (70 to 800F).
NOTE:
Sample must be cooled to less than 100ºF (38ºC) to prevent high test results.
Sample must be protected from air contact while cooling to prevent low test results.
1. Measure 50 ml of the water sample with the graduated cylinder . For error free result Collect water to be tested in a clean, preferably large-mouthed, bottle to overflowing. Immediately cap and cool to room temperature.
2. Add three or four drops of TK - 13 ::: RXSOL-62-5503-002 to the sample Swirl to mix. Sample should turn red.
3. Add TK - 14 ::: RXSOL-62-5503-003 Powder a dipper at a time, swirling after each dipper, until color changes from red to colorless. Add 2 more dippers. Swirl until dissolved. ( Note : Use the plastic dipper to add TK - 14 ::: RXSOL-62-5503-003 to the sample. Add only one measure at a time and stir thoroughly between each addition of TK - 14 ::: RXSOL-62-5503-003. All the particle of TK - 14 ::: RXSOL-62-5503-003 may not dissolve and this may create a slight haze in the sample. Continue to add the TK - 14 in this manner until the red color disappears. It is not necessary that the sample solution be exactly neutralized, only that the sample turn colorless. When the sample is colorless, add one additional measure of TK - 14 ::: RXSOL-62-5503-003 and stir. )
4. Add TK - 15 ::: RXSOL-62-5503-004 Reagent dropwise, swirling and counting after each drop, until color changes from colorless to a faint but permanent blue. Always hold bottle in vertical position.
This color change is taken as the endpoint. Record the ml of TK - 15 ::: RXSOL-62-5503-004 solution used.
Calculation of Results
FORMULA: ppm sulfite as SO3 = ml of TK - 15 ::: RXSOL-62-5503-004 x 500 / ml SAMPLE
Using a 50 ml sample, sulfite, in parts per million as SO3 is equal to the ml of TK - 15 ::: RXSOL-62-5503-004 required multiplied by 10.
Limitations of Test :::
This method is rapid and adaptable to field determinations. It is affected by any oxidizable substances in the water such as organic matter sulfides and nitrites. The presence of these interfering substances will cause the sulfite content obtained from this titration to by shown as a higher value than actually exists.
|
Also we are keeping ready stock of these products :
SODIUM SULPHATE 99% WHITE POWDER CRYSTAL 50 KG BAG
PHOSPHORIC ACID 85% WHITE LIQUID POWDER
Caustic Soda Lye
HYDROGEN PEROXIDE 50% LIQUID 35 KG CARBOY PACK
CITRIC ACID 99% POWDER
caustic soda flakes
BLEACHING POWDER
SODIUM NITRATE
ACETIC ACID
Synonym: Sulfurous Acid, Disodium Salt
Chemical Name: Sulfurous acid, Disodium salt
Chemical Formula: Na2So3
#SodiumSulphite_UnitedArabEmiratesDubai
#SodiumSulphite_MuscatOman
#SodiumSulphite_MumbaiVizagKolkataChennaiGandhidham
Sodium Metabisulfite supplier and exporter. Sodium Metabisulphite also called sodium pyro sulphite. Food grade of Sodium sulphite is used as preservative agent, reducing agent, Antibrowning agent, antioxidant, flour treatment agent also as preservative in biscuit industries.
We are keeping ready stock of Sodium Metabisulfite in 25 Kg and 50 Kg pack. And we are one of popular sodium metabisulphite supplier in Mumbai, Kandla - Gandhidham, Chennai - Ennore, Visakhapatnam, Kolkata, Fujairah, Dubai, Sharjah, Abu Dhabi, Sodium Sulphite supplier in Barka Ruwi Muscat Oman
Sodium Metabisulfite is White crystals or crystalline powder having an odour of sulfur dioxide
HOW to TEST purity of Sodium Sulfite?
PURITY TESTS
Reagents: Hydrochloric acid, hydrazinium sulfate, standard selenium solution (100µg Se/ml)
Procedure
Weigh 2.0 ± 0.1 g of sample and transfer to a 50-ml beaker. Add 10 ml water, 5 ml hydrochloric acid and boil to remove SO2.
Into a second beaker, weigh 1.0 ± 0.1 g of sample, add 0.05 ml standard selenium solution and proceed as above.
To each beaker add 2 g hydrazinium sulfate and warm to dissolve. Let stand for 5 min. Dilute the contents of each beaker to 50 ml in a Nessler tube and compare the colour of the two solutions. The sample should be less pink than the sample with the added standard.
METHOD OF ASSAY
Weigh 0.2 g of the sample to the nearest mg, add to 50.0 ml of 0.1 N iodine in a glass-stoppered flask, and stopper the flask. Allow to stand for 5 min, add 1 ml of hydrochloric acid, and titrate the excess iodine with 0.1 N sodium thiosulfate, adding starch TS as the indicator. Each ml of 0.1 N iodine is equivalent to 4.753 mg of Na2S2O5.
Oxygen Control
Chemical Oxygen Scavengers. The oxygen scavengers most commonly used in boiler systems are sodium sulfite, sodium bisulfite, hydrazine, catalyzed versions of the sulfites and hydrazine, and organic oxygen scavengers, such as hydroquinone and ascorbate.
It is of critical importance to select and properly use the best chemical oxygen scavenger for a given system. Major factors that determine the best oxygen scavenger for a particular application include reaction speed, residence time in the system, operating temperature and pressure, and feedwater pH. Interferences with the scavenger/oxygen reaction, decomposition products, and reactions with metals in the system are also important factors. Other contributing factors include the use of feedwater for attemperation, the presence of economizers in the system, and the end use of the steam. Chemical oxygen scavengers should be fed to allow ample time for the scavenger/oxygen reaction to occur. The deaerator storage system and the feedwater storage tank are commonly used feed points.
In boilers operating below 1,000 psig, sodium sulfite and a concentrated liquid solution of catalyzed sodium bisulfite are the most commonly used materials for chemical deaeration due to low cost and ease of handling and testing. The oxygen scavenging property of sodium sulfite is illustrated by the following reaction:
2Na2SO3 | + | O2 | ® | 2Na2SO4 |
sodium sulfite | oxygen | sodium sulfate |
Theoretically, 7.88 ppm of chemically pure sodium sulfite is required to remove 1.0 ppm of dissolved oxygen. However, due to the use of technical grades of sodium sulfite, combined with handling and blowdown losses during normal plant operation, approximately 10 lb of sodium sulfite per pound of oxygen is usually required. The concentration of excess sulfite maintained in the feedwater or boiler water also affects the sulfite requirement.
Sodium sulfite must be fed continuously for maximum oxygen removal. Usually, the most suitable point of application is the drop leg between the deaerator and the storage compartment. Where hot process softeners are followed by hot zeolite units, an additional feed is recommended at the filter effluent of the hot process units (prior to the zeolite softeners) to protect the ion exchange resin and softener shells.
As with any oxygen scavenging reaction, many factors affect the speed of the sulfite-oxygen reaction. These factors include temperature, pH, initial concentration of oxygen scavenger, initial concentration of dissolved oxygen, and catalytic or inhibiting effects. The most important factor is temperature. As temperature increases, reaction time decreases; in general, every 18°F increase in temperature doubles reaction speed. At temperatures of 212°F and above, the reaction is rapid. Overfeed of sodium sulfite also increases reaction rate. The reaction proceeds most rapidly at pH values in the range of 8.5-10.0.
The following operational conditions necessitate the use of catalyzed sodium sulfite:
- low feedwater temperature
- incomplete mechanical deaeration
- rapid reaction required to prevent pitting in the system
- short residence time
- use of economizers
High feedwater sulfite residuals and pH values above 8.5 should be maintained in the feedwater to help protect the economizer from oxygen attack.
Some natural waters contain materials that can inhibit the oxygen/sulfite reaction. For example, trace organic materials in a surface supply used for makeup water can reduce speed of scavenger/oxygen reaction time. The same problem can occur where contaminated condensate is used as a portion of the boiler feedwater. The organic materials complex metals (natural or formulated catalysts) and prevent them from increasing the rate of reaction.
Sodium sulfite must be fed where it will not contaminate feedwater to be used for attemporation or desuperheating. This prevents the addition of solids to the steam.
At operating pressures of 1,000 psig and higher, hydrazine or organic oxygen scavengers are normally used in place of sulfite. In these applications, the increased dissolved solids contributed by sodium sulfate (the product of the sodium sulfite-oxygen reaction) can become a significant problem. Also, sulfite decomposes in high-pressure boilers to form sulfur dioxide (SO2) and hydrogen sulfide (H2S). Both of these gases can cause corrosion in the return condensate system and have been reported to contribute to stress corrosion cracking in turbines. Hydrazine has been used for years as an oxygen scave