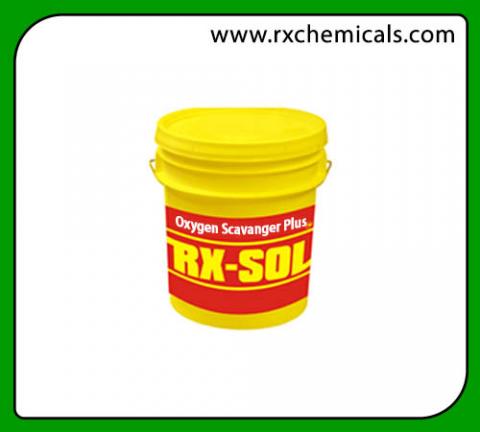
Oxygen Remover Scavanger Plus
Oxygen Remover Scavanger Plus is a catalysed liquid solution of Hydrazine and diethylhydroxylamine (DEHA). Its volatile properties ensure distribution throughout the boiler and condensate system, and hence protects against oxygen corrosion in all parts of the system. The product also provides the required conditions for the establishment of a passivating layer of magnetite on all inner surfaces. RXSOL-50-5022-025 is a low toxicity product, suitable for high, medium and low pressure boiler systems.
RXSOL-50-5022-025 The objective is to maintain a hydrazine residual between 0.05-0.2 ppm depending on operating pressure and boiler designe. Actual consumption is determined under operating conditions. A normal dosage is approximately 1 ltr. per day, depending of system layout.
Hydrazine is a convenient reductant because the by-products are typically nitrogen gas and water. Thus, it is used as an ANTIOXIDANT, an oxygen scavenger, and a corrosion inhibitor in water boilers and heating systems.
Hydrazine is mainly used as a foaming agent in preparing polymer foams
TESTING PROCEDURE ::: http://rxmarine.com/hydrazine-test-kit
Directions for use
This product is formulated for use in conjunction. Oxygen Scavenger Plus can be used in any boiler system, and in conjunction with mechanical deaeration systems. Removal of dissolved oxygen is vital for prevention of corrosion and especially pitting corrosion in boilers. When dosed into a boiler system, Oxygen Scavenger Plus will react with dissolved oxygen and form non corrosive compounds. The product is volatile, and left over product from oxygen scavenging in the pre-boiler section will evaporate and assist protection of the steam and condensate system. No solid materials are produced when using Oxygen Remover Scavanger Plus.
Dosing method
Rx Marine International recommends continuously into the boiler feed line and Boiler Water Treatment Dosing Unit.
Dosing should be controlled so that the DEHA residual in the condensate is between 0.08-0,30 ppm. The consumption will depend on feed water temperature and the amount of water fed into the boiler. For more information about initial dosage and dose rate please consult your nearest Customer Centre.
Test result condensate PPM DEHA
0.00 - 0.08 0.08 - 0.30 0.30 +
Increase dose 25% Maintain dose Decrease dose 25%
Sampling and testing
A representative sample of Condensate should be drawn for analysis daily. The sample should always be taken from the same sampling point, cooled and tested immediately By Rxsol Test Kit. It is important that regular testing is carried out, to ensure the correct level of treatment is maintained.
Features
• Fast acting, liquid oxygen scavenger.
• Safe and easy to use, low toxicity.
• Reduces corrosion of iron and copper, increasing system life and reliability.
• Neutralises acids occurring in condensate system.
• Volatile product, provides distribution and protection throughout the boiler system, economical in use.
• Suitable for use in conjunction with combined and co-ordinated treatment programmes.
• Organic product, no dissolved solids added.
• Simple test to determine treatment level.
Product Specifications: | |
Density |
1 |
Packing, Type |
PLASTIC |
Volume |
25 l |
pH |
10.5 |
Colour |
LIGHT YELLOW |
Appearance |
LIQUID |
Directions for use
This product is formulated for use in conjunction.Oxygen Scavenger Plus can be used in any boiler system, and in conjunction with mechanical deaeration systems. Removal of dissolved oxygen is vital for prevention of corrosion and especially pitting corrosion in boilers. When dosed into a boiler system, Oxygen Scavenger Plus will react with dissolved oxygen and form non corrosive compounds. The product is volatile, and left over product from oxygen scavenging in the pre-boiler section will evaporate and assist protection of the steam and condensate system. No solid materials are produced when using Oxygen Scavenger Plus.
Dosing method
Rx Marine International recommends continuously into the boiler feed line and Boiler Water Treatment Dosing Unit.
Dosing should be controlled so that the DEHA residual in the condensate is between 0.08-0,30 ppm. The consumption will depend on feed water temperature and the amount of water fed into the boiler. For more information about initial dosage and dose rate please consult your nearest Customer Centre.
Test result condensate PPM DEHA
0.00 - 0.08 0.08 - 0.30 0.30 +
Increase dose 25% Maintain dose Decrease dose 25%
Sampling and testing
A representative sample of Condensate should be drawn for analysis daily. The sample should always be taken from the same sampling point, cooled and tested immediately By Rxsol Test Kit. It is important that regular testing is carried out, to ensure the correct level of treatment is maintained.
Features
• Fast acting, liquid oxygen scavenger.
• Safe and easy to use, low toxicity.
• Reduces corrosion of iron and copper, increasing system life and reliability.
• Neutralises acids occurring in condensate system.
• Volatile product, provides distribution and protection throughout the boiler system, economical in use.
• Suitable for use in conjunction with combined and co-ordinated treatment programmes.
• Organic product, no dissolved solids added.
• Simple test to determine treatment level.
Where Hydrazine Test Kit used ?
HYDRAZINE TEST KIT is used for the determination of Hydrazine content in the Boiler’s Water. The test must be performed when in the vessel’s Boiler Water Treatment used hydrazine ingredient to control rust and corrosion RXSOL-50-5022-025 / RXSOL-50-5007-025 / RXSOL-19-1541-025. This is an activated hydrazine solution (Hydrazine with a catalyst for faster reaction with Dissolved Oxygen,) and applied for marine and industrial Boilers in low, medium and high pressures.
Oxygen Remover Scavanger Plus manufacturer, exporter and supplier in Mumbai, Gandhidham Kandla, Chennai Ennore, Kolkata Haldia, Vizag Visakhapatnam, Paradip, Haldia, Fujairah, Dubai, Ajman, Sharjah, ABudhabi, Muscat Oman, Canada BC
The establishment of protective metal oxide lay-ers through the use of reducing agents (such as hydrazine, hydroquinone, and other oxygen scavengers) is known as metal passivation or metal conditioning. Although "metal passivation" refers to the direct reaction of the compound with the metal oxide and "metal conditioning" more broadly refers to the promotion of a protective surface, the two terms are frequently used interchangeably.
The reaction of hydrazine and hydroquinone, which leads to the passivation of iron-based metals, proceeds according to the following reactions:
N2H4 | + | 6Fe2O3 | ® | 4Fe3O4 | + | 2H2O | + | N2 |
hydrazine | hematite | magnetite | water | nitrogen |
C6H4(OH)2 | + | 3Fe2O3 | ® | 2Fe3O4 | + | C6H4O2 | + | H2O |
hydroquinone | hematite | magnetite | benzoquinone | water |
Similar reactions occur with copper-based metals:
N2H4 | + | 4CuO | ® | 2Cu2O | + | 2H2O | + | N2 |
hydrazine | cupric oxide | cuprous oxide | water | nitrogen |
C6H6O2 | + | 2CuO | ® | Cu2O | + | C6H4O2 | + | H2O |
hydroquinone | cupric oxide | cuprous oxide | benzoquinone | water |
Magnetite and cuprous oxide form protective films on the metal surface. Because these oxides are formed under reducing conditions, removal of the dissolved oxygen from boiler feedwater and condensate promotes their formation. The effective application of oxygen scavengers indirectly leads to passivated metal surfaces and less metal oxide transport to the boiler whether or not the scavenger reacts directly with the metal surface.